The author is an agricultural engineer for USDA-NRCS.
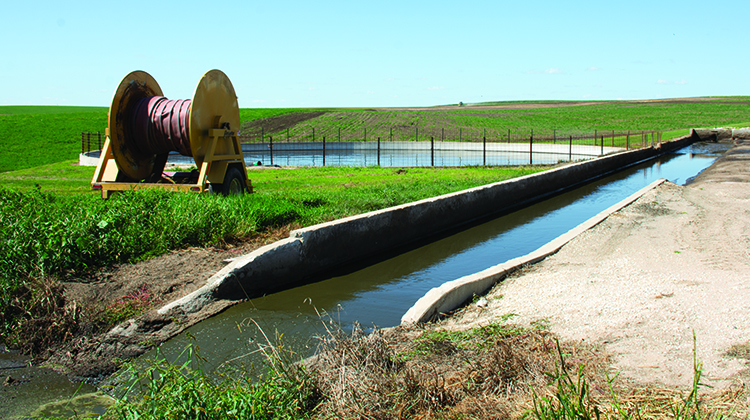
As dairy farms grow in herd size, the amount of required bedding also goes up. Dairy farmers often use sand as bedding because of its availability, comfort, and effectiveness in maintaining herd udder health.
With farms using as much as 100 tons of sand weekly, any type of sand recovery could be a substantial money saver. To recycle this bedding, sand settling lanes are becoming more prevalent in the dairy industry.
In Illinois, we have seen a surge in this type of system, and as with any new process, producers have experienced some trouble getting the settling lanes to perform as intended. In evaluating the sand settling lanes, it was found that most of the problems had to do with the operation and maintenance of the system.
Takes effort to operate
Dairy farmers are always busy, and time is at a premium. Most do not want another structure on-site that requires more time to operate. Producers may assume that a sand settling lane is a “plug and play” system. Unfortunately, this is not the case. Sand settling lanes require continual operation and maintenance to function properly.
In 2016, we visited five Illinois dairy farms with sand settling lanes. Various parameters were measured to see how the sand lanes were functioning. During the visits, the producers shared information about their operation and maintenance.
Most were never given operation and maintenance instructions, which meant they had to determine how to run the sand lane on their own. Because of this, the sand lanes at each of these facilities were not separating the maximum amount of sand out of the waste stream. This led to excessive sand in the waste storage facility at the end of the sand lane and the producer having to purchase extra sand for bedding.
How to do it
From this small field study, we recommend that the producer understands the following key features before the sand settling lane is put into operation. This way, the sand lane functions at its optimal performance.
Know the system’s capacity (both flow rate and velocity of the waste stream). Every sand lane is designed for a certain flow rate or capacity. The flow rate is determined by the time it takes the waste stream (coming from the flush system of the freestall barn) to go through the sand lane and the dimensions (length and cross-section area) of the sand lane.
For sand to settle, the waste stream needs to be at an optimal velocity — not too fast and not too slow. When the velocity is correct, sand will settle in the sand lane and solid manure particles will continue to be suspended in the liquid (see Figure 1).
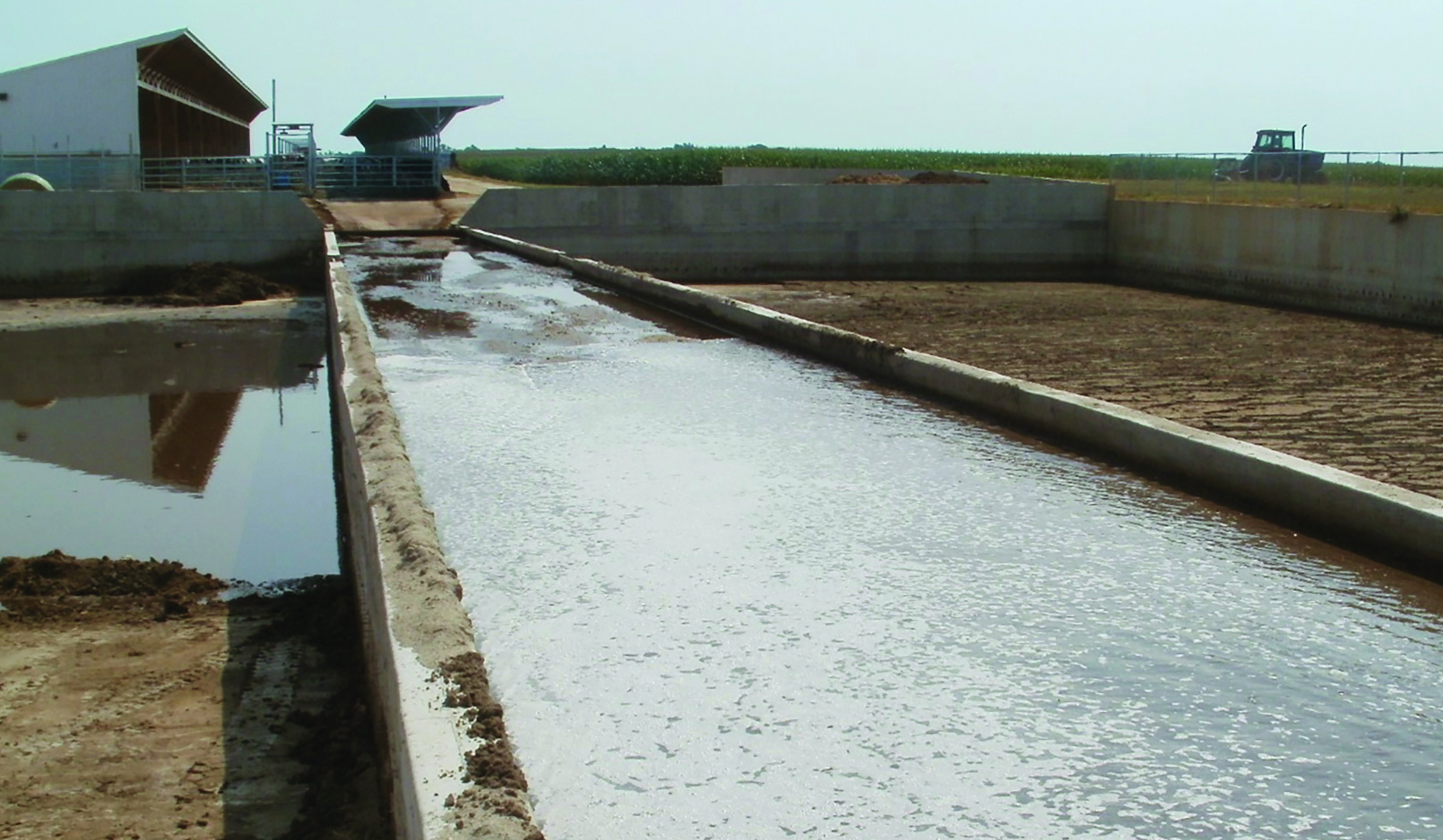
Changing the flow rate (or velocity) of the flush system will impact the effectiveness of the sand settling lane. The producer needs to know the optimal flow rate for the sand settling lane so that it can be set and not changed. In general, the optimal flow velocity is between 1 and 2 feet per second, depending on the size of the sand particles.
Knowing the length of the sand lane (in feet) and measuring how long the waste stream takes to travel this length (in seconds) will determine velocity. It is advisable to measure the velocity of the waste stream weekly to make sure that nothing has changed with the flush system.
Regular cleaning is necessary. Many producers do not realize that the sand lane needs to be cleaned daily. When a sand lane is working effectively, sand is being deposited in the lane. The deposited sand affects the flow dynamics in the settling lane by changing the cross-sectional area of the flush lane or by reducing the effective slope. These changes in cross-sectional area and slope can significantly affect the amount of sand that will settle in the lane.
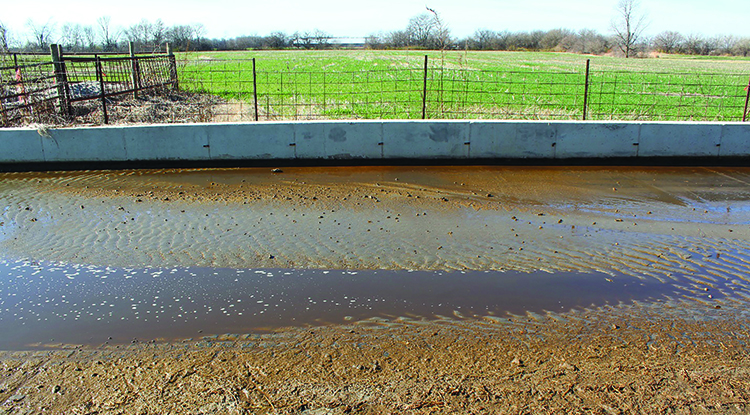
If a producer cleans the sand out of the lane only once or twice a week, the buildup of sand between the clean-outs lowers the effectiveness of the sand settling lane (see Figure 2). Since sand settling lanes are typically designed for flow with no additional sand in the lane, cleaning the sand settling lane daily is important to maximize the collection of sand in the lane.
Management of the reclaimed sand that is removed from the settling lane is important as well. To reuse the sand as bedding, this sand needs to be cleaned. The sand particles still contain some manure and wastewater that can cause mastitis.
When the sand is removed from the sand settling lane, it is usually placed in a sand storage area for about three months (see Figure 3). This will allow enough time for rainfall to clean the recovered sand if the sand pile is turned weekly so that all of the sand can be cleaned by the rain. If the stored sand is simply left until it is time to be reused as bedding, this will raise the risk of mammary infections for the milking cows.
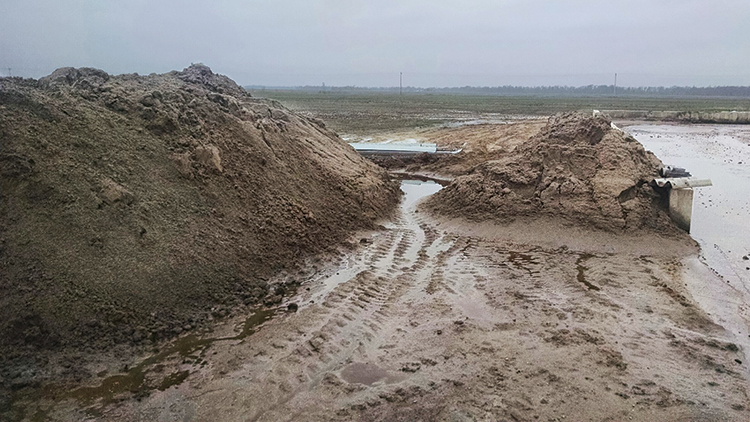
Follow the plan
When a sand settling lane is built, ask the designer of the system for an operation and maintenance (O&M) plan. The O&M plan should include all the above items, along with seasonal (or annual) maintenance items.
Following a site-specific O&M plan is recommended to maximize the effectiveness of the system. With the large economic investment to have a sand settling lane designed and constructed, it only makes sense to keep it running with optimal performance to maximize the return on investment.
This article appeared in the November 2020 issue of Journal of Nutrient Management on pages 20 and 21.
Not a subscriber? Click to get the print magazine.