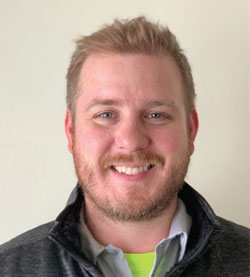
Some farmers want their nutrients mixed across the whole soil profile. Others want the nutrients in zones as to disturb the soil profile as little as possible.
The minimum disturbance method has been a hurdle because we need to meet the higher rates of application with all the water being collected on these farms. To do that, we need to have soil available to absorb the nutrients we are applying.
It seems there is no one tool that fits all situations. In hilly conditions, one piece of equipment might not work because the nutrients will move down the zones and blow out at the bottom of the hill, potentially causing runoff. Some work better when there is a little moisture to soften the soil, making it easier to penetrate compaction. Some shank units, if used when conditions are wetter, will smear the trench and won’t allow absorption either, which could cause nitrogen striping. Some pieces won’t allow more than 15,000 gallons per acre because they don’t go deep enough.
I’ve been to many field days across the country and have seen different machines work great in soil that makes every applicator look like a rock star. In real life, 95% of the time conditions are never perfect, and we need to work in many different field situations.
In my search for the perfect machine, I stumbled across a unit that works best for me, and it is versatile. I have a bar applicator that is 44 feet wide, and we added a row unit made by TK Ag Works in southern Wisconsin. The bar is wide, so I can use it for topdress applications like a dribble bar if I want. I can also easily change out coulters to go from less aggressive to more aggressive tillage. The unit has been built heavy for the rigors of custom application and is low maintenance with greaseless bearings.
This machine is also capable of high rates. The coulter unit runs straight and has steel fins that are about 3 inches wide. When they enter the ground, they go in vertical, and as the coulter rotates, the fins leave the soil horizontal. This lifts the soil profile, pulling up compaction and leaving a nice, soft zone that is perfect to absorb liquid nutrients.
The coulter has a serrated edge as well so there is no need for a lead coulter. This allows for residue to flow or be chopped up, it does not plug the row unit, and it reduces weight. By using this row unit we find the growers are back in their fields far sooner than when we disturb the entire soil profile. I’m not saying that we don’t have disks and rippers in our yard, but we are trying to move away from those if we can.
As have many other nutrient applicators this year, we also added the John Deere HarvestLab 3000 with Constituent Sensing to this bar. We are able to apply nutrients based on many different criteria, like real-time values for total nitrogen, ammonia nitrogen, potassium, phosphorous, and dry matter.
"In my search for the perfect machine, I stumbled across a unit that works best for me, and it is versatile."
In the past, we were given a rate for a field, and we put the same rate on the entire field. With all the restrictions on fields today, a field with a limitation will lump the whole field into that rate. If we can prove what is put where with this technology, we can apply a higher rate on parts of the field. The technology will speed up and slow down the tractor as you cross those zones in the field. This makes it possible to apply variable rate manure on the fly — and do it accurately.
This year we are trying a lot of new tools and working with our growers to utilize this technology to its fullest potential. We want to make sure the storage pits are empty at the end of the year and that our customers are more profitable by utilizing the nutrients they produce on farm to the maximum extent possible.
This article appeared in the August 2020 issue of Journal of Nutrient Management on page 24.
Not a subscriber? Click to get the print magazine.